Across the country, bucket trucks have become an essential part of infrastructure development and maintenance. These versatile vehicles support a wide array of industries, from utility and telecom to municipal work and emergency response. As explained by Scott Stoneham, their ability to safely elevate workers and tools makes them invaluable for tasks that demand precision at height. As infrastructure demands grow with new projects and technologies, the design and functionality of bucket trucks have also advanced, boosting safety and efficiency on job sites.
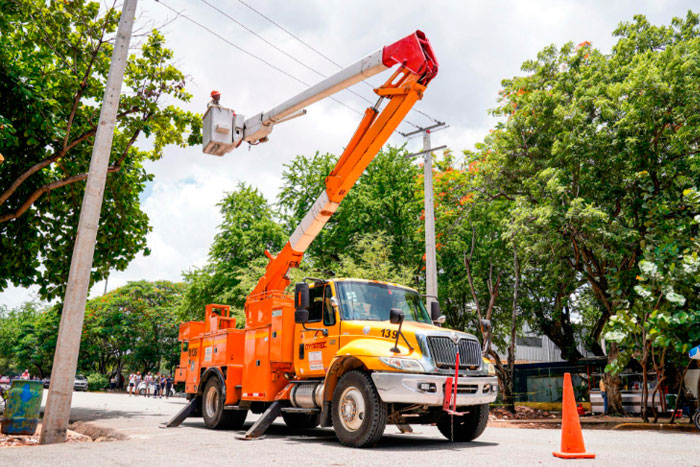
Regulatory compliance, including OSHA and ANSI standards, ensures these machines operate within strict safety parameters, safeguarding crews and the public alike. From smart diagnostics to electric powertrains, innovation continues to shape the future of bucket trucks, allowing them to meet the challenges of tomorrow’s infrastructure with greater adaptability and reliability.
Bucket Trucks
Bucket trucks, also known as aerial lift trucks or cherry pickers, are specialized vehicles designed to lift workers safely and their tools to elevated heights. These vehicles are widely used across industries that handle above-ground infrastructure. Utility companies depend on them for line maintenance and installation. Telecom crews use them to expand network coverage on poles and towers, while construction teams rely on them for structural work at height.
In sectors where safe and efficient vertical access is necessary, bucket trucks have become a standard part of the fleet. Their ability to quickly position personnel and equipment above ground level allows teams to complete tasks with greater control and fewer risks. Crews can also reduce downtime since the setup process is far quicker than with traditional scaffolding.
Supporting Sectors Across the Country
Bucket trucks are indispensable to electrical utility companies, especially during the maintenance of power lines and the installation of new grid components. Crews can reach high-voltage lines safely while keeping traffic disruptions minimal. These trucks enable precise work in elevated positions, which is vital when handling complex wiring or switching out transformers on active lines.
Telecommunications teams also rely heavily on bucket trucks to access aerial fiber lines and install 5G equipment on poles and towers. With the nationwide push to expand broadband access, particularly in rural and underserved communities, the demand for aerial work has surged. These trucks allow crews to complete installations quickly while maintaining safety protocols.
Beyond utilities, municipalities regularly employ bucket trucks to handle streetlight repairs, traffic signal maintenance, and the upkeep of public signage. Their reach and maneuverability allow workers to perform tasks efficiently without the need to block roads for long periods. Even tree trimming and vegetation control near critical infrastructure benefit from the accessibility that bucket trucks provide. In colder climates, they are also used to clear ice from overhead lines during winter storms.
Built-in Safety and Jobsite Efficiency
One of the most noteworthy advantages of bucket trucks is the ability to carry out aerial tasks without resorting to ladders or erecting scaffolding, both of which pose greater risks and require more setup time. By lifting workers in a secured platform, the chance of falls is greatly reduced, making the jobsite safer for everyone involved. This not only protects workers but also limits liability for employers.
Modern bucket trucks come equipped with features that enhance safety and productivity. Insulated booms protect workers from electrical hazards, while harness attachment points and stabilizing outriggers ensure the vehicle remains steady during operation. These design elements allow crews to focus on their tasks with fewer interruptions and lower risk. Some models even come with automatic leveling systems to ensure platform balance on uneven ground.
The efficiency gains are also notable. Crews can move between job sites quickly and adjust their working height with precision, completing more assignments in a single day. This not only improves project timelines but also reduces labor costs and equipment downtime. In densely populated urban settings, this mobility can be the difference between a one-hour repair and a major delay.
Advances in Design and Technology
Modern bucket trucks have grown well beyond their early mechanical designs. Today’s models incorporate advanced hydraulic controls, allowing operators to make smooth, precise movements even in tight or elevated spaces. Some units now include smart diagnostics systems that alert crews to potential mechanical issues before they become serious problems, increasing uptime and safety.
Environmental impact is also being addressed through the development of electric and hybrid bucket trucks. These newer models reduce emissions and noise, making them ideal for urban settings or projects in environmentally sensitive areas. In cities with strict emissions standards, such vehicles are helping companies meet regulatory goals without sacrificing performance. Charging capabilities and battery range continue to improve, enabling longer workdays on a single charge.
Customization has become another key feature in newer fleets. Specialized attachments, such as articulated arms or tool racks, enable teams to tailor trucks for specific tasks like tree trimming, sign replacement, or heavy-duty construction support, further expanding their versatility.
Operator Standards and Regulations
Operating a bucket truck requires more than just a standard driver’s license. Workers must complete proper training and certification programs to ensure they know how to safely control and maintain the equipment. These programs often include both classroom instruction and hands-on experience.
Regulatory agencies such as OSHA and ANSI provide detailed guidelines that govern how aerial lift equipment should be used on job sites. These standards cover everything from equipment inspection schedules to fall protection requirements. Adhering to them isn’t optional—it’s integral for legal compliance and worker safety. Regular inspections, daily and periodic, are conducted to catch wear and tear before it leads to failure.